Email Enquiry - RE: ABB 'The Specialist' - Low Pressure Storage Tank Vents
Subject:
Date
of Initial Email : 20 January 2010
Initial Email Detail:
We at ABB Engineering Services have produced a technical bulletin to share good practice and learning within the process industries.
The main philosophy is to provide technical information and guidance that practising engineers and managers would find useful. Ideally we would like to share learning and experiences, ours and yours, from around the world, in a way that will not draw attention to a specific company, so getting away from the various litigation issues and other sensitivities. By acting through this independent channel we can all share our learning responsibly and anonymously!.
Storage tanks have been in the news recently - failures have had significant consequences for safety, health and the environment and because of the size of their inventories, a loss of containment can represent a major business impact. Storage tanks are primarily regarded as "low pressure" and their pressure relief requirements tend to be given less attention than their primary containment features. This month's Specialist focuses on the importance of ensuring that adequate in-breathing and out-breathing is provided and maintained. [Specialist not attached to email]
Second Email: 21 January
I am not so sure about this guidance and have my own reservations on this especially the comment regarding justifying the installation of a flame arrestor.
In my opinion a collapsed tank is a smaller consequence than a tank that explodes, surely the flame arrestor should be on a rigorous inspection routine to ensure that it doesn’t block.
I would send a note of caution out to members about this one!
Third Email: 21 January
JOIFF RESPONSE:
I guess that is why they are suggesting that The new API will reflect the ISO and that Flame Arrestors should be included in new design
ABB suggesting looking at risk assessing current systems and new systems falling in line with the new standards. Is it your position that all such valves should undergo retrospective change out?
Your right however the consequences any be significantly different in each case...
Fourth Email: 21 January
MEMBER RESPONSE:
In my opinion the justification for the installation of a flame arrestor should be based on the acceptance criteria related to the consequence of a tank explosion and not a tank collapse. I don’t think these two separate issues should be linked and one judged against the other.
To prevent a tank collapse the removal of another safety device which in my opinion offers a higher reduction of consequence should not even be considered.
Two independent consequences with different prevention solutions.
Tank collapse – One should consider all measures to prevent the breather vents from being ineffective
If the vent becomes blocked, you may experience a tank collapse and worst case have a release of HC inside a bunded area which has been designed as the secondary level of protection.
Losses - Cost of clean up and new tank, minimal business disruption
Tank explosion – One should consider all measures to prevent ignition entering the tank
If the flame arrestor is removed and ignition enters the tank due to flashback, tank explodes, significant damage, almost certain a large fire will follow which could have secondary effects for other process tanks and the remaining facility.
Losses – Tank destroyed, fuel destroyed, other process equipment damaged, major disruption of business and significant risk to personnel, firefighters and the environment etc.
It’s not just for new designs, under DSEAR regulations UK, ATEX 137 Europe and many other international standards, these risk should be considered independently and assessed against their probability and consequence and managed against an acceptance criteria.
All breathers, safety valves and arrestors on existing tanks should be reviewed to confirm that they are effective and if they are installed in the first place, if they are not then you need to consider if this is an acceptable risk to take. These are very simple applications and if they are not effective pose a significant risk, it’s not a massive capital outlay to assess all tanks in your facility and to maintain or to make improvements as required, the risk reduction from doing such assessments and improvements will be huge.
If these measures are not addressed I think it would be very difficult to defend the statement that risk had been reduced ‘As Low As Reasonably Practicable’
Minimal cost for flame arrestor and minimal cost for inclusion onto maintenance inspection system.
It’s what we all call a No Brainer!!
Just my opinion and may not follow the opinion of others.
Fifth Email: 24 January 2010
JOIFF RESPONSE:
Many thanks for the note.
When you state in your note re; Tank Collapse 'Losses - Cost of clean up and new tank, minimal business disruption' I guess there is differing risks depending on what material is stored. I know their were specific conditions and circumstances relating to how the vapour cloud was generated at Buncefield, however low flash material in a bund resulting from tank collapse may provide me with more to think about than a high flash material.
I engaged ABB once again with your previous note (anonymously) suggesting a JOIFF member had a different view on the topic. I attach below response from their senior process safety engineer:
The comment back from JOIFF was
"I am not so sure about this guidance and have my own reservations on this especially the comment regarding justifying the installation of a flame arrestor. In my opinion a collapsed tank is a smaller consequence than a tank that explodes, surely the flame arrestor should be on a rigorous inspection routine to ensure that it doesn’t block."
The answer to this is one of engineering judgement and balancing the likelihood of failure against the consequences. Until recently the guidance on attaching flame arresters to pressure vacuum valves on low pressure storage tanks was mixed but it is probably fair to say that it was waited towards not fitting them unless there was good reason to do so. This guidance was in API 2000 and HSG 176.
The ISO 28300 guide has changed the guidance on flame arresters with the following text from section 5.4.2
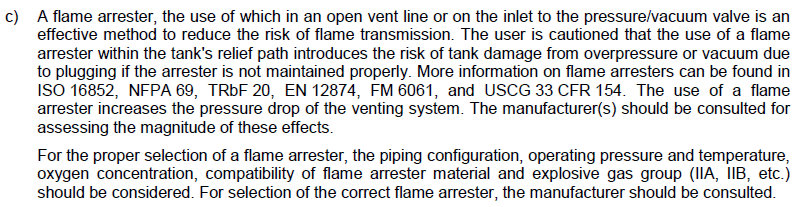


Therefore the perceived wisdom that a flame could not pass through a PV valve is wrong as it has been demonstrated that flames can pass through them, although the words "at least at the tested conditions" suggests that the group who wrote the guide were not convinced that under real conditions rather than test conditions this could occur. However the guidance at this point seems fairly clear but then the guide follows with the following statement again from section 4.5.4
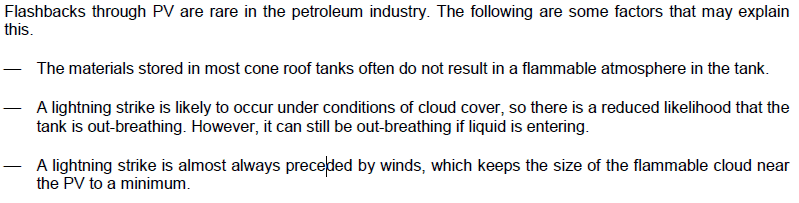
To me, and I admit this is my opinion, this is the guide stepping back from definitively saying put flame arresters with PV valves. It says that there is not a history of flammable low pressure storage tank exploding due to flashback. Then there is the consideration of what could be the source of ignition. Typically there is very little on the top of the tank that is a source of ignition and the guide is suggesting that the most likely cause is a lightening strike. However in stormy conditions it is unlikely that a flammable atmosphere will be there because of the wind and the probability that the tank will be inbreathing at this point.
The guidance from current guidance from EEMUA is
"Extract from EEMUA 159 Users' Guide for Inspection, Maintenance and Repair of Storage Tanks:"
11.3.5 Flame Arresters
Flame arresters are devices for preventing passage of a flame while permitting the flow
of gas or vapour, and are sometimes installed in pressure-vacuum valves to prevent a
flame entering the tank. However the small apertures of a flame arrester can easily
become blocked, thereby reducing the effectiveness of the PN valve. Tests with PN
valves have demonstrated that the flow of vapour through a valve is sufficient to
prevent a flame entering the tank so that the flame arresters are not necessary. (A
valve would not be inbreathing in an external fire situation.)
This philosophy and the test work is described in detail in Petroleum Safety Data PSD
2210 in the article ‘Flame Arresters for Tank Vents’, published by the American
Petroleum Institute in May 1971, which states:
There is no supportable basis for requiring that an outdoor, above-ground tank provided
with a PV-valve must also be equipped with a flame arrester. The use of flame arresters is discouraged unless the user is willing and able to institute the maintenance necessary
to ensure that the required venting capacity is maintained.
(The quoted publication has been superseded by API RP 2210 Flame Arresters forVents of Tanks Storing Petroleum Products, June 2000.)
The second part to this issue is the flame arrester itself and is highlighted in the EEMUA guidance. The problem with these devices is that they get forgotten and not maintained in many cases and the problem then is that they block and cause a tank to be sucked in potentially releasing the whole tank contents into the bund. If the flame arrester is put on the safety critical device register then it should be well maintained and blocking should not occur. The other issue to consider is do you retrofit or do you apply this guidance only to new vessels. Flame arresters naturally have a pressure drop across them so it may not be possible to simply install them on existing vents as this may reduce their capacity below the required levels.
The other piece of information I have on this is an anecdote from the Pressure Relief courses we run where one of the delegates had asked the HSE this question and their response to him was to not put the flame arrester on. Obviously I don't know the full details of his particular application but from the conversation we had this was the HSE advise. I understand the HSE are discussing some of issues raised in ISO 28300 and hopefully guidance will be published.
Trying to sum all of this up as I said before it is an engineering judgement. In our experience flame arresters do get forgotten and not maintained so the likelihood of collapsing a tank is higher than the likelihood of getting a flame through a pv valve and exploding the tank. On the other hand the consequences of exploding a tank are more serious that collapsing a tank. although a collapsed flammable storage may well release all of its' contents into the bund and despite zoning there may be an ignition source and this incident will also be serious. Our general judgement has come down on the side of not fitting flame arresters unless there is a good reason.
I hope this answers the question, but if not please feel free to contact me
Sixth Email: 25 January 2010
INITIAL MEMBER'S RESPONSE:
Thanks for the feedback,
Again I am never comfortable with the argument that because People forget to do things we shouldn’t use these things a basis of safety. Quite often people try and find fixes to new problems when they don’t try and fix the original cause, it appears here that a rigorous audited inspection schedule for flame arrestors would provide a much reduced level of risk.
If I owned a facility and wanted to protect my business and employees I would either create a very robust system to ensure maintenance did not slip and if the safety item is so critical I would consider installing two of them as dual redundancy, I wouldn’t consider accepting the risk of either a tank collapse or explosion.
Again it comes down to the cost and I don’t think that improvements to maintenance or dual redundancy in this instance prohibit the reduction of risk afforded by such measures.
I am sure we could discuss all night, this is what happens when we remove prescriptive measures and work in a self evaluated society. Evaluations will differ and some will undoubtedly be better than others.
It’s good to discuss these points through and challenge our own personal judgment from time to time. |