Process Safety Beacon: Does the piping meet the specification?
A vapor cloud explosion and fire led to one fatality and two serious injuries. At least 28 other workers were injured. About 10,000 lb. (4500 kg.) of flammable isobutylene was released when a 3-inch (75mm) Y-strainer failed, likely due to thermal expansion. The vapor cloud ignited causing an explosion.
This Beacon focuses on using piping materials approved in the pipe specification.
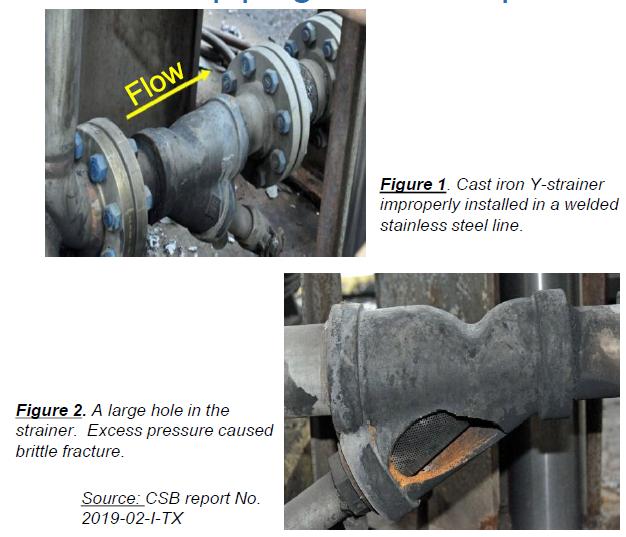
The Piping and Instrumentation Diagram (P&ID) for the piping had several errors. It didn’t show the Y-strainer, a check-valve nor a manual isolation valve. A Process Hazards Analysis (PHA) was performed when the system was installed and was revalidated about a year before the accident. No one noted that the P&ID did not match the field piping. According to the drawing, the piping was welded or flanged 304 stainless steel. The 3-inch diameter cast iron Y-strainer was connected to the stainless steel line using threaded joints. Most industry pipe specifications would certainly prohibit 3-inch threaded connections in isobutylene service.
Cast metal devices, like this strainer, are more brittle than stainless steel. They can fail and are specifically prohibited in pressurized hydrocarbon service by several industry piping standards.
Did you know?
- Design of new piping systems should follow industry-approved piping specifications. They provide guidance for temperature, pressure and correct materials.
- Most companies have internal piping specifications for various process and utility fluid services.
- If your company doesn’t have its own piping specifications, groups like Process Industry Practices (PIP), American Society of Mechanical Engineers (ASME), European Committee for Iron and Steel Standardization (ECISS), and Japanese Industrial Standards Committee (JISC) have standards that can be adopted by the company.
- Threaded connections are seldom used in larger diameter hazardous service piping. They may be
used for small diameter instrument or sampling connections. - Any deviation from pipe specifications should require a Management of Change review that includes an analysis of the modification by a technical team.
- All piping installations should have a Prestart-up Safety review (PSSR) to ensure the piping meets
the correct specification.
What can you do?
- The P&IDs should accurately show the process piping as it exists in the field. If they do not, report
it to your supervisor. - A good practice is for the PHA facilitator to field – check the accuracy of the P&ID’s prior to starting
the study. - If you see any threaded connections (over 3/4 inch (19 mm) diameter) in hazardous service, report it to your supervisor so they can be checked.
- If a piping change is needed, use the company’s MOC system so the proper reviews are performed.
Featured Stock Image Credit: EntirelySafe
Case Credit: Process Safety Beacon